Im Rahmen des Sondermaschinenbaus lieferte HEIKO Metallbau eine vollautomatische Wachsplattenanlage an einen ungarischen Kunden aus. Die Anlage, welche in der Lage ist bis zu 3,5t Wachse oder Paraphine pro Stunde zu kühlen, wurde von HEIKO Metallbau entwickelt, konstruiert, ausgeliefert und in Betrieb genommen.
Von der Schmelze zur Kartonware – Konfektionierung von Wachsplatten
Mit einer im Rahmen des Sonderanlagenbaus für eine osteuropäische Raffinerie entwickelten Anlage von HEIKO Metallbau ist es möglich, mit einer Leistung von 3,5 t/Std im 7/24 Betrieb kontinuierlich schmelzflüssig vorgelegte Mikro- und Makrowachse vor zu kühlen und dann mit Coriolis Durchflussmessgeräten gewichtstoleranzgenau in einem breiten Viskositätsbereich in rechteckige flache Wannen abzufüllen, die anschließend in einem Kühltunnel über ein endloses Kettenförderband über mehrere Ebenen bis zum Biegewechsel der Anlage transportiert und hierbei verfestigt werden, wonach im Anschluss die Entleerung der Wannen auf einem Förderband in eine Kartonverpackungsanlage erfolgt. Die Anlage ist mit Rezepturhinterlegung komplett SPS gesteuert. Das Konzept lässt sich auch auf zahlreiche andere Produkte übertragen, mit allen Vorteilen bezüglich Staubvermeidung, Schüttgewichtseinstellung und optimaler Nutzung des benötigten Raums für Transport und Lagerung durch das Endprodukt.
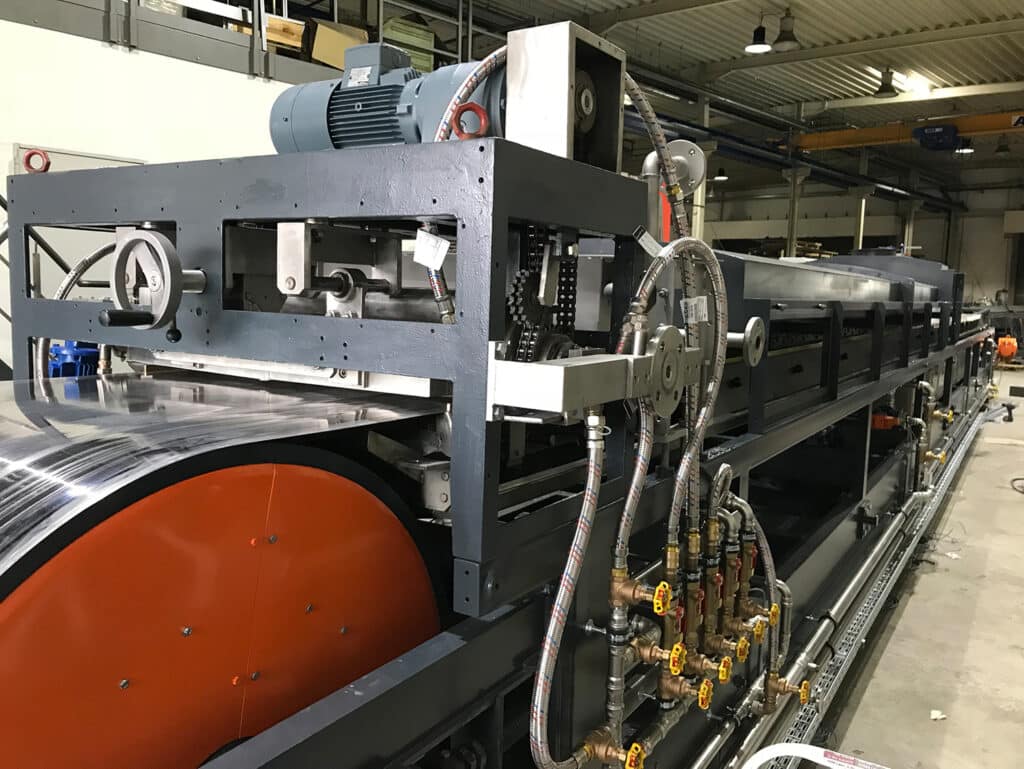
Kontinuierliche Herstellung von gewichtsgenauen Wachsplatten
Die Leistung kann entweder über die Viskosität und die Temperatur des Produktes, die Fördergeschwindigkeit, die Kaltlufttemperatur oder die Durchflussmenge angepasst werden. Die Abfüllung erfolgt jeweils mit einem Gewicht von 5 kg +- 0,5% Toleranz pro Wanne basierend auf einer Abkühlzeit von durchschnittlich 120 – 180 Minuten, wobei die Verweilzeit im Kühltunnel auf Grundlage der spezifischen Wärmekoeffizienten des Produktes erfolgt, welches üblicherweise in einem Dichtebereich von 0,7 – 0,9 g/ml liegt. Die Entladungstemperatur, die erforderlich ist, um das Verpacken von festen Platten zu ermöglichen, liegt in der Regel bei 20-22°C. Das Produkt wird zunächst mit 20-25°C über dem Schmelzpunkt anfallend in einer Vorkühleinrichtung auf 7-10°C über dem Schmelzpunkt abgekühlt. Beim Eintritt in den Kühltunnel liegt das Produkt dann noch bei 5-7°C über dem Schmelzpunkt. Um eine optimale und zugleich möglichst rasche Kühlung des Produktes sicherzustellen, soll das Wachs immer den Vorkühler mit einer Temperatur so dicht wie möglich über dem jeweiligen Schmelzpunkt verlassen, um die benötigte Kühlzeit im Kühltunnel zu reduzieren und die Befüllung der Wannen zugleich so hochviskos wie möglich zu ermöglichen.
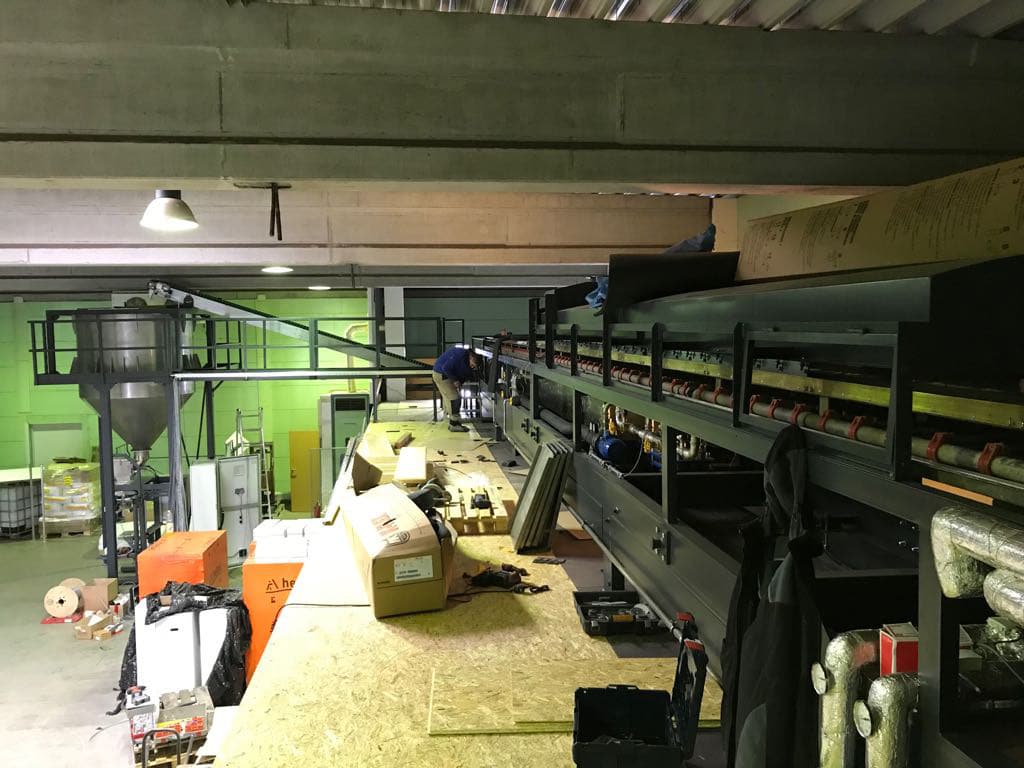
Alle mit dem Produkt in Berührung kommenden Teile sind entweder aus Edelstahl V4A oder bei nicht-metallischen Werkstoffen aus FDA-zugelassenen Werkstoffen. Die reguläre Geschwindigkeit des Kettenförderbandes von 1,1-1,2 m/Min lässt sich den individuellen rheologischen Eigenschaften des Produktes anpassen. Die Anlage enthält 1.710 Wannen in 6 reihiger Anordnung und zwecks rückstandsfreier Entleerung polierter Ausführung mit einer Größe von 490 x 290 mm, die mittels der SPS in Bezug auf Fördergeschwindigkeit, Dauer der Abkühlzeit und Höhe der Platten je nach Dichte des Produkts einstellbar sind.
Kühlung und Steuerung als besondere technischen Herausforderungen
Unterschiedliche Produkte benötigen unterschiedliche Kühlzeiten, wofür der frequenzgesteuerte Motor für die Förderung der Wannen im Kühltunnel über die SPS-Steuerung einstellbar ist. Die Bewegung der Wannen im Kühltunnel erfolgt über eine endlose Trägerkette entlang der Schienen vertikal über 12 Ebenen. Sobald die Wannen die Oberseite der Maschine erreicht haben, gelangen sie aus dem isolierten Sandwichpanelgehäuse der Anlage, wo sie umgedreht werden und der erstarrte Block seitlich auf einen Bandförderer in Richtung der Verpackungseinheit abgeführt wird. Der Tunnel besteht insgesamt aus 12 Stufen, die für die Kühlung vorgesehen und als Kühllabyrinth mit paralleler Führung der zu kühlenden Wannenreihen konzipiert sind.
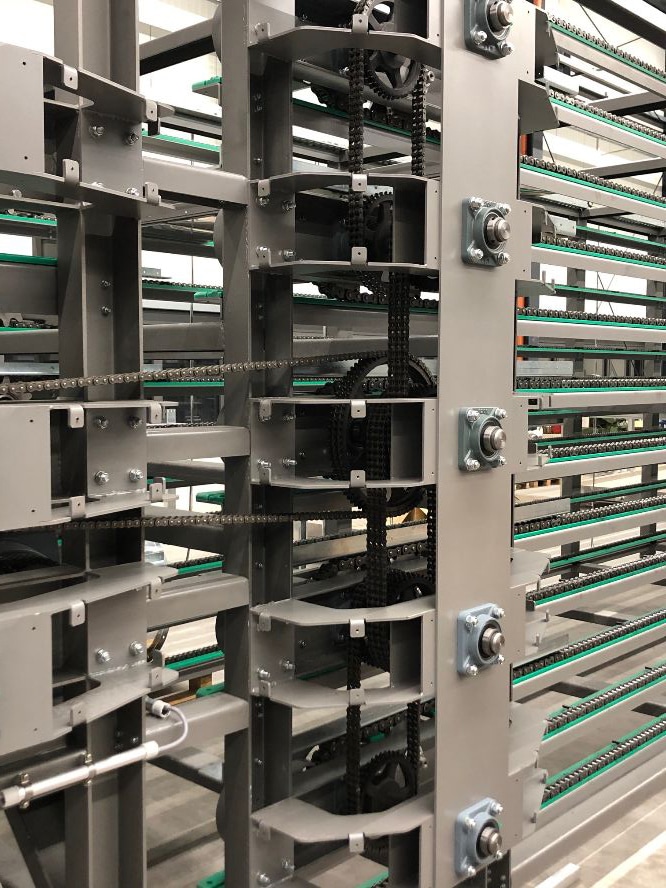
Die Kühleinheit zur Bereitstellung der benötigten Kühlluft wird mit flüssigem Ammoniak bei -10°C betrieben wird, um eine ausreichende Kühlung durch die Luft zu gewährleisten, die im Inneren des Systems zirkuliert. Hierzu werden 3 Lamellenwärmetauscher mit 6 Ventilatoren und einer Leistung von 3 x 170 kW und mit einem Volumenstrom von 3 x 50000 m³/Std eingesetzt. Während die Wannen durch die Anlage transportiert werden, wird kalte Luft eingebracht, wodurch dem Produkt die Wärme entzogen wird. Die eingebrachte Kaltluft wird über Führungsleisten, Leitbleche, Kanäle und Trichter im Kühltunnel verteilt, die seitlich installiert werden, um die Luft in einer definierten Weise mit einer sanften Luftzirkulation auf die Platten zu blasen und um hierbei zu vermeiden, dass Deformationen an den Oberflächen der späteren Platten entstehen. Die durchschnittliche Lufttemperatur wird in allen Phasen des Kühlprozesses jederzeit mit 0,5-8,5°C gewährleistet.
Die SPS basiert auf Simatic S 7 mit in TIA entwickelter Anwendungssoftware und regelt die Temperaturen von Produkt, Heiz- und Kühlmedien, Wasser, Luft und Ammoniak sowie die einzelnen Prozessschritte über die Verarbeitungsgeschwindigkeiten der einzelnen Komponenten und die jeweiligen Verweilzeiten in einem kontinuierlichen vollautomatischen Prozess mit Hinterlegung von Rezepturen und der Option, frei wählbare weitere Rezepturen jederzeit einpflegen zu können.
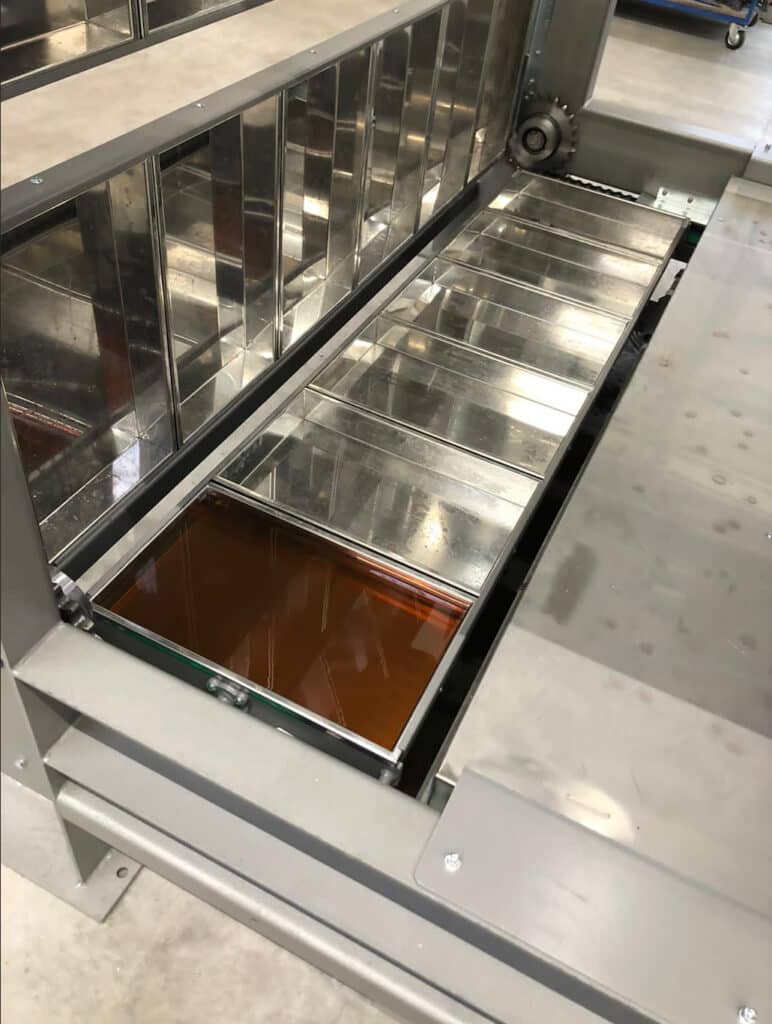
Ausblick
Automatisierung und gleichzeitige strikte Einhaltung von Spezifikationen und Normen als Folge gestiegener Anforderungen an Produktqualität und Arbeitssicherheit geben dem Sonderanlagenbau international neue Perspektiven – die hier vorgestellte Anlage ist dafür ein gutes Beispiel.
Weitere Informationen und einen detailierteren Bericht der Fachpresse finden Sie unter dem folgenden Link.
Autoren: Heiko Spiering, geschäftsführender Inhaber von Heiko Metallbau und Anton Klassen, Leiter Verfahrenstechnik bei Heiko Metallbau