Within the scope of special machine construction, HEIKO Metallbau delivered a fully automatic wax plate plant to a Hungarian customer. The plant, which is capable of cooling up to 3.5t of waxes or paraphines per hour, was developed, designed, delivered and commissioned by HEIKO Metallbau.
From the melt into the cardboard box – Confectioning of wax sheets
With a plant developed by HEIKO Metallbau as part of the special engineering for an Eastern European refinery, it is possible to continuously pre-cool molten micro and macro waxes at a rate of 3.5 t/h in 7/24 operation and then fill them into rectangular flat tubs with Coriolis flowmeters with exact weight tolerances in a wide viscosity range. These are then transported in a cooling tunnel via an endless chain conveyor belt over several levels to the bending station of the line, where they are solidified, after which the tubs are discharged on a conveyor belt into a carton packaging line. The line is completely PLC controlled with recipe storage. The concept can also be applied to numerous other products, with all the advantages in terms of dust prevention, bulk density adjustment and optimum use of the space required for transport and storage by the end product.
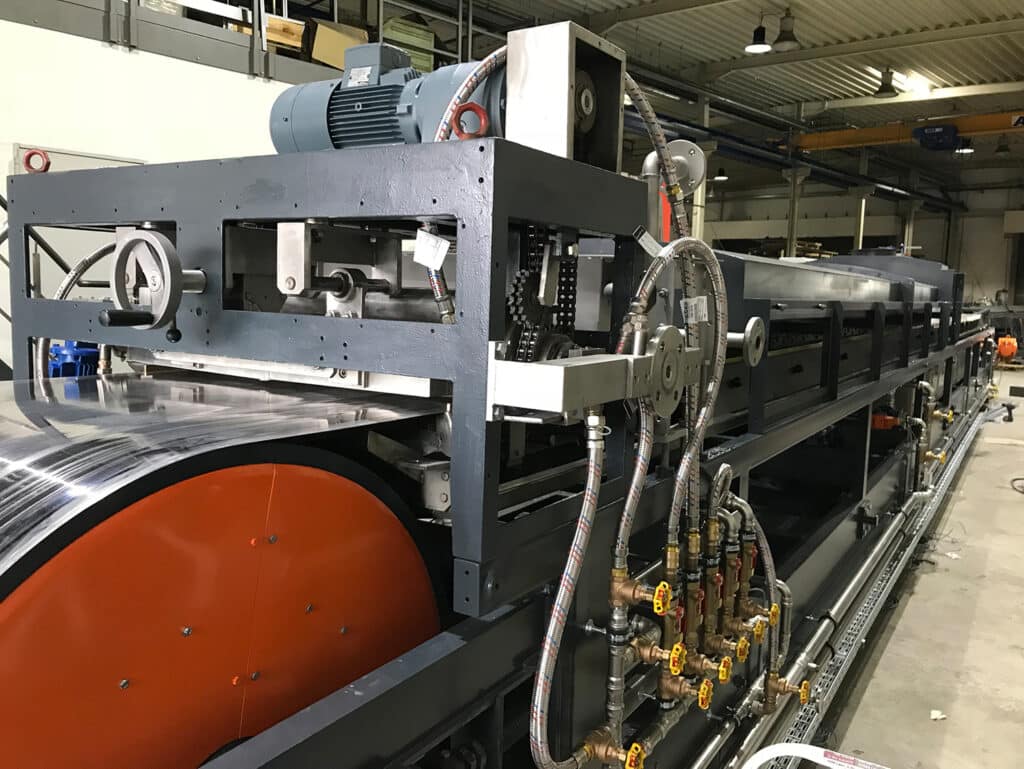
Continuous production of wax plates with accurate weights
The capacity can be adjusted either by the viscosity and temperature of the product, the conveying speed, the cold air temperature or the flow rate. In each case, filling is done with a weight of 5 kg +- 0.5% tolerance per vat based on a cooling time of 120 – 180 minutes on average, with the residence time in the cooling tunnel based on the specific heat coefficients of the product, which is typically in a density range of 0.7 – 0.9 g/ml. The discharge temperature required to enable solid sheet packaging is typically 20-22°C. The product is first cooled to 7-10°C above the melting point in a pre-cooling unit at 20-25°C above the melting point. On entering the cooling tunnel, the product is then still 5-7°C above the melting point. In order to ensure optimum and at the same time rapid cooling of the product, the wax should always leave the pre-cooler at a temperature as close as possible above the respective melting point in order to reduce the cooling time required in the cooling tunnel and at the same time allow the tubs to be filled with as high a viscosity as possible.
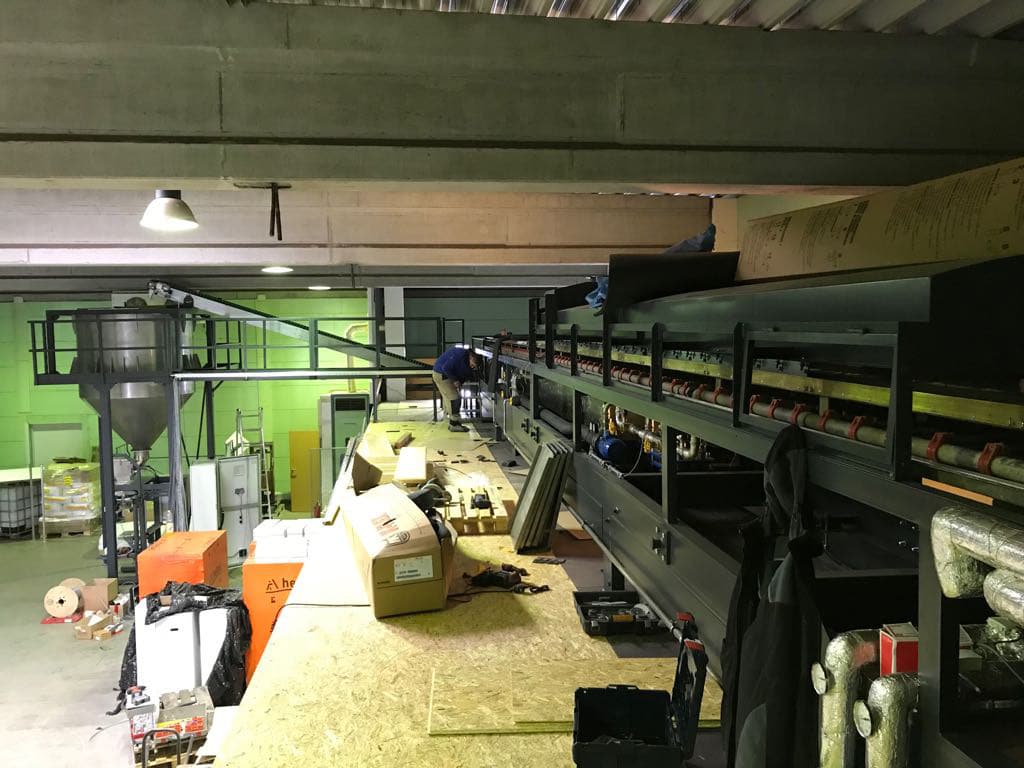
All parts in contact with the product are either made of V4A stainless steel or, in the case of non-metallic materials, of FDA-approved materials. The regular speed of the chain conveyor belt of 1.1-1.2 m/min can be adjusted to the individual rheological properties of the product. The line contains 1,710 trays in a 6-row arrangement and polished for residue-free discharge, with a size of 490 x 290 mm, adjustable by means of the PLC in terms of conveying speed, duration of cooling time and height of the plates according to the density of the product.
Cooling and control as special technical challenges
Different products require different cooling times, for which the frequency-controlled motor for conveying the tubs in the cooling tunnel can be adjusted via the PLC control. The tubs in the cooling tunnel are moved vertically over 12 levels via an endless carrier chain along the rails. Once the tubs reach the top of the machine, they exit the insulated sandwich panel enclosure of the system, where they are inverted and the solidified ingot is discharged laterally onto a belt conveyor towards the packaging unit. The tunnel consists of a total of 12 stages provided for cooling and designed as a cooling labyrinth with parallel guidance of the rows of trays to be cooled.
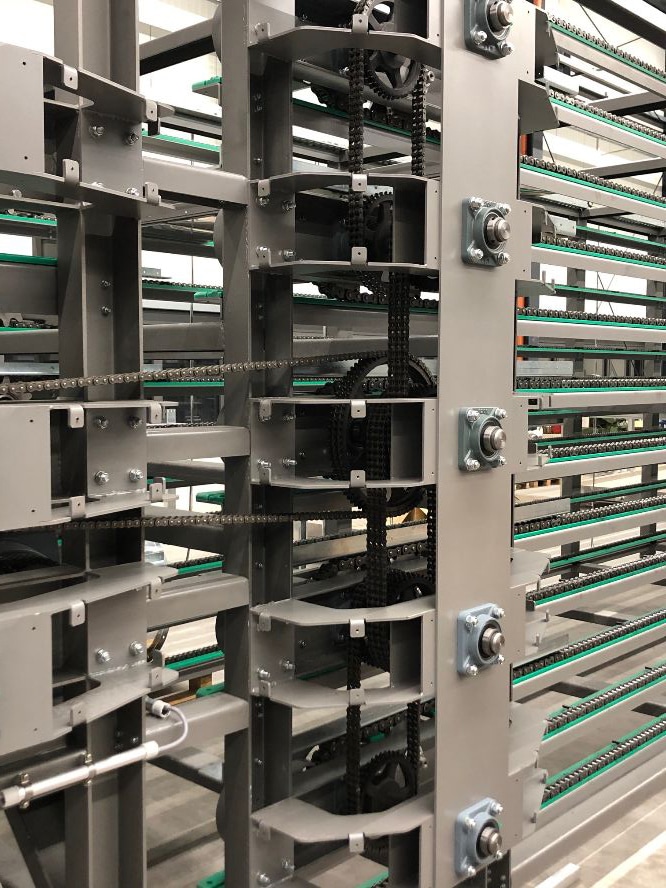
The cooling unit for providing the required cooling air is operated with liquid ammonia at -10°C to ensure sufficient cooling by the air circulating inside the system. For this purpose, 3 finned heat exchangers with 6 fans and a power of 3 x 170 kW and with a flow rate of 3 x 50000 m³/h are used. While the tubs are transported through the system, cold air is introduced, extracting the heat from the product. The cold air introduced is distributed in the cooling tunnel through guide rails, baffles, ducts and hoppers installed laterally to blow the air onto the panels in a defined way with a gentle air circulation, avoiding deformations on the surfaces of the subsequent panels. The average air temperature is guaranteed at 0.5-8.5°C at all times during all phases of the cooling process.
The PLC is based on Simatic S 7 with application software developed in TIA and controls the temperatures of product, heating and cooling media, water, air and ammonia as well as the individual process steps via the processing speeds of the individual components and the respective dwell times in a continuous fully automatic process with storage of recipes and the option of being able to enter freely selectable additional recipes at any time.
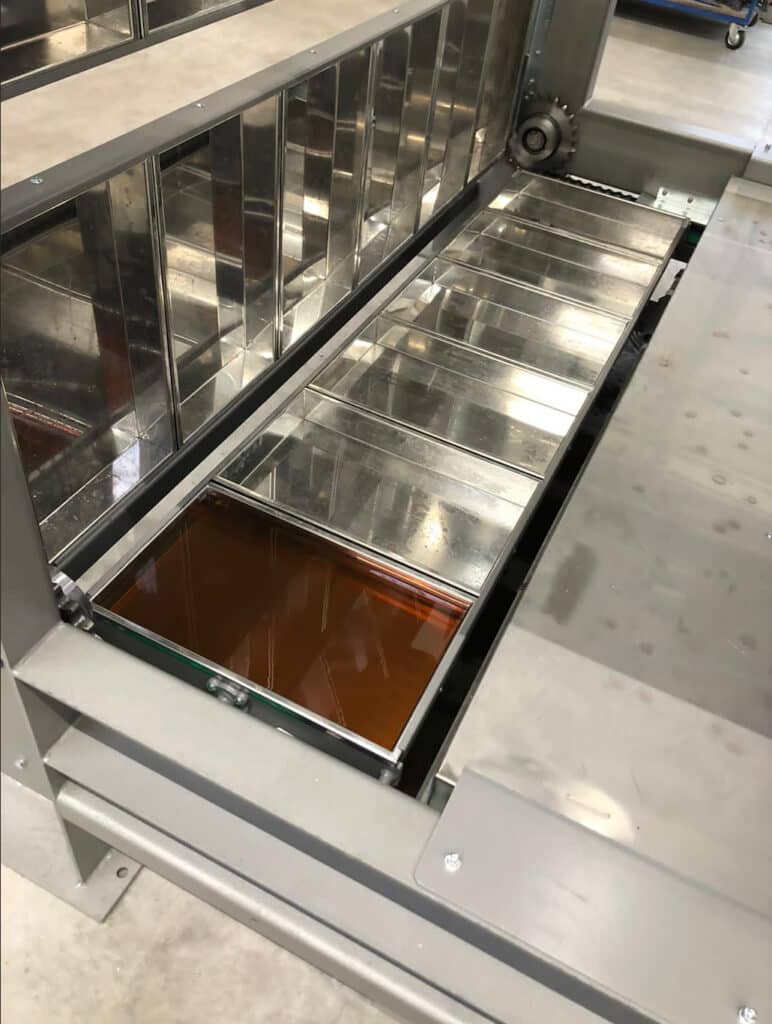
Outlook
Automation and simultaneous strict compliance with specifications and standards as a result of increased demands on product quality and occupational safety are opening up new perspectives for special plant engineering internationally – the plant presented here is a good example of this.
Further information and a more detailed report from the trade press can be found under the following link.
Authors: Heiko Spiering, Managing owner of HEIKO Metallbau und Anton Klassen, Process engineering manager at HEIKO Metallbau